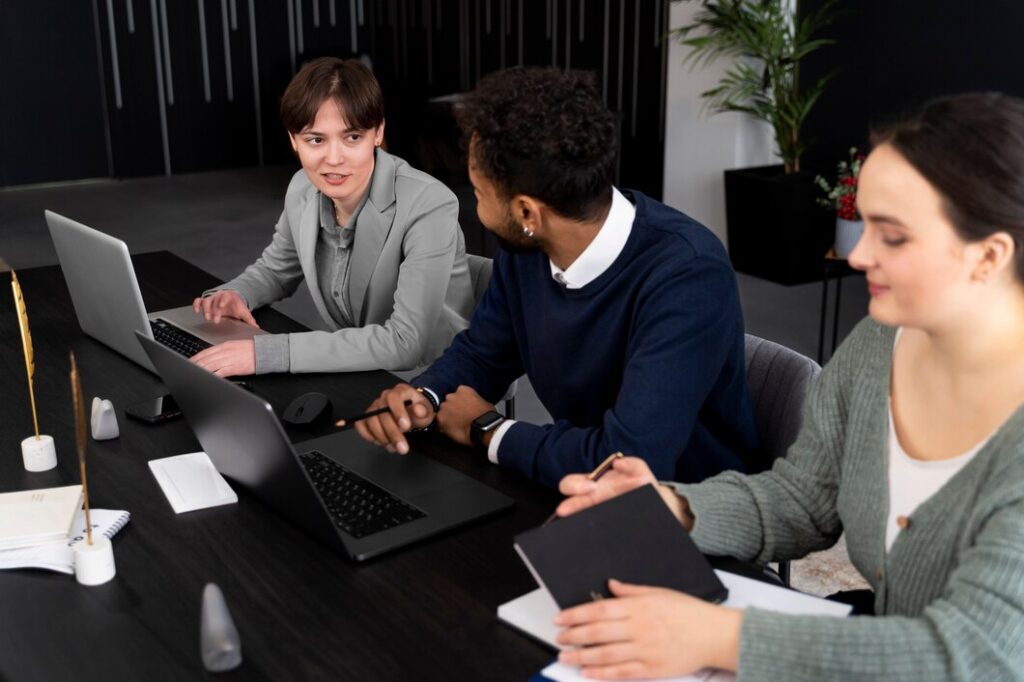
Tips for Identifying the Perfect ERP Software for Manufacturing Operations
Choosing the right Enterprise Resource Planning (ERP) software for manufacturing operations is one of the most critical decisions a company can make. An effective ERP system can streamline processes, enhance productivity, and provide real-time data insights that are essential for informed decision-making. This article provides comprehensive tips to help you identify the perfect ERP software for your manufacturing operations, ensuring that you make a well-informed choice that aligns with your business needs.
1. Define Your Specific Requirements
Assess Current Challenges
Before you begin evaluating different ERP systems, take the time to assess your current operations and identify any challenges or inefficiencies. Consider factors such as:
- Inventory Management: How do you currently manage inventory levels, and what issues do you face? Are there frequent stockouts or overstock situations?
- Production Planning: How do you schedule production runs? Is there a need for better forecasting and planning tools?
- Compliance and Quality Control: What regulations does your business need to adhere to, and how can ERP software help ensure compliance?
- Reporting Needs: What type of data and reports do you require for decision-making?
Create a Wish List
After identifying challenges, create a list of must-have features and functionalities that the ERP software should provide. This list might include:
- Real-time tracking of inventory and production
- Advanced analytics and reporting capabilities
- Integration with existing tools (like CRM or supply chain management software)
- Customizable dashboards
2. Evaluate Industry-Specific Solutions
Manufacturing is a diverse sector with unique requirements that vary by industry. When evaluating ERP solutions, prioritize those designed specifically for manufacturing businesses. Industry-specific solutions often include tailored features that can address challenges such as:
- Lean Manufacturing: Tools for optimizing production processes and reducing waste.
- Supply Chain Management: Modules for managing supplier relationships and logistics.
- Quality Assurance: Systems to monitor quality control processes and compliance with industry standards.
Explore Vendor Expertise
Research the vendors’ backgrounds and expertise in manufacturing. Look for companies with a proven track record in providing ERP solutions to similar industries. Read case studies, testimonials, and reviews to gauge their effectiveness.
3. Consider Scalability
Your business may not remain the same size indefinitely; therefore, it’s vital to select an ERP system that can grow with you. Assess the scalability of the software in terms of:
- User Capacity: Can the system handle more users as your team expands?
- Functionality: Are additional modules or features available for future needs?
- Geographical Expansion: If you plan to expand internationally, can the software support multi-currency and multi-language features?
Investing in a scalable solution today can save you from costly migrations in the future.
4. Assess Integration Capabilities
An ERP system should not operate in isolation. It must integrate seamlessly with your existing software systems, such as Customer Relationship Management (CRM), Human Resources Management (HRM), and Supply Chain Management (SCM) tools. Consider the following:
- Data Flow: How well will data flow between systems? Will integration require manual intervention or additional software?
- APIs and Middleware: Does the ERP software provide APIs or middleware solutions to facilitate integration with other systems?
5. Prioritize User Experience
User adoption is critical to the success of any ERP implementation. A system that is difficult to navigate will hinder productivity and lead to frustration. To ensure a positive user experience:
Evaluate User Interface Design
- Intuitive Layout: Look for software that features a clean and intuitive layout that is easy to navigate.
- Customization: Check if users can customize their dashboards to display the information most relevant to them.
Training and Support
- Training Resources: Ensure that the vendor provides comprehensive training materials and support for users to help them adapt to the new system.
- User Community: A strong user community can provide additional support, tips, and resources to help users maximize the software’s capabilities.
6. Look for Customization Options
Every manufacturing operation has unique processes and workflows. Therefore, choose ERP software that allows for customization to fit your specific needs. Consider the following aspects of customization:
- Modular Design: Opt for a system with a modular design, allowing you to add or remove features as needed.
- Custom Workflows: Ensure that you can customize workflows and processes to align with your operational requirements.
7. Check Vendor Support and Training
Vendor support is critical during the implementation phase and beyond. Assess the following aspects of vendor support:
Level of Support
- Availability: Is support available 24/7? How quickly can you expect responses to inquiries?
- Types of Support: Does the vendor offer multiple support channels, such as phone, email, or chat?
Training Programs
- Implementation Training: Verify that the vendor provides comprehensive training during the implementation phase to help users understand the system.
- Ongoing Training: Consider vendors that offer ongoing training sessions or resources to keep your team updated on new features.
8. Read Reviews and Case Studies
Before making a final decision, take the time to read reviews and case studies from other manufacturers. These resources can provide valuable insights into how different ERP systems perform in real-world scenarios. Pay attention to:
- User Experiences: Look for common themes in user experiences, both positive and negative.
- Success Stories: Identify case studies that highlight significant improvements in efficiency or productivity after implementing a particular ERP system.
9. Request a Demo
Before committing to an ERP system, request a demo to experience the software firsthand. A demo will allow you to:
- Test Features: Explore the features and functionalities that are most important to your operations.
- Evaluate User Interface: Assess the user interface and navigation to determine if it aligns with your expectations.
- Ask Questions: Use the demo as an opportunity to ask the vendor questions about specific functionalities and how they can meet your needs.
10. Analyze Total Cost of Ownership
Understanding the total cost of ownership (TCO) is critical for making an informed decision. TCO includes not only the initial licensing fees but also ongoing costs such as:
- Implementation Costs: Consider costs associated with setting up the system, including any necessary hardware.
- Maintenance Fees: Assess any maintenance or subscription fees that will be incurred over time.
- Training Costs: Factor in expenses related to training your team to use the new software.
Evaluating TCO will help you understand the full financial impact of your ERP decision and ensure it aligns with your budget.
Conclusion
Identifying the perfect ERP software for your manufacturing operations requires careful consideration and evaluation of various factors. By defining your specific requirements, assessing industry-specific solutions, considering scalability, and prioritizing user experience, you can make a well-informed decision that enhances productivity and streamlines operations. Additionally, understanding the importance of integration, customization options, vendor support, and total cost of ownership will further guide you toward selecting the ideal ERP system that meets your business needs. With the right ERP solution in place, your manufacturing operations can thrive and adapt to the challenges of an ever-evolving market.